What Is The Difference Between Screen Printing And Flexographic Printing?
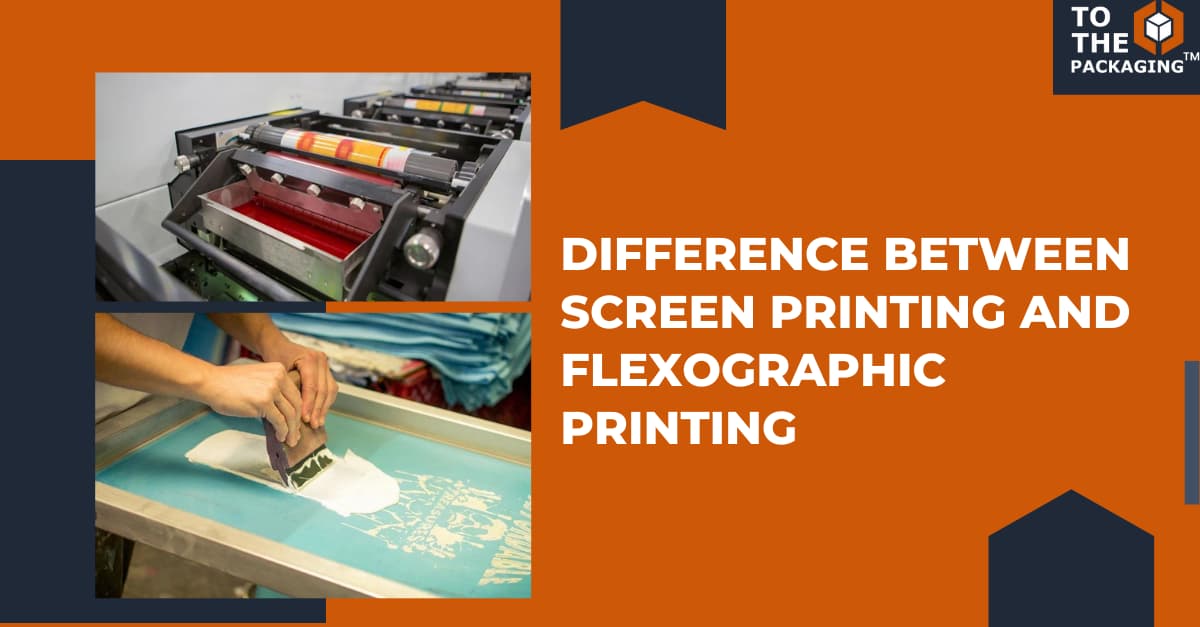
When we are involved in advertising or other business that requires printing. It is better to do some research on the subject before making a silly and expensive mistake.
As there are many types of printing techniques available in the market, how do we know which one of them would be right for us?
To ease this confusion, we have a blog that will explain the difference between these two types of printing techniques that are popular in the printing market.
After explaining the difference between these two printing techniques. We will discuss the advantages of these two printing styles so that you get a clear idea of what each printing technique is.
Which one is a better pick for you?
If that is something that you are interested in learning then stay with us and keep reading.
What Is The Screen Printing Process?
Screen printing uses stencils on a mesh to push the paint or ink onto the desired surface.
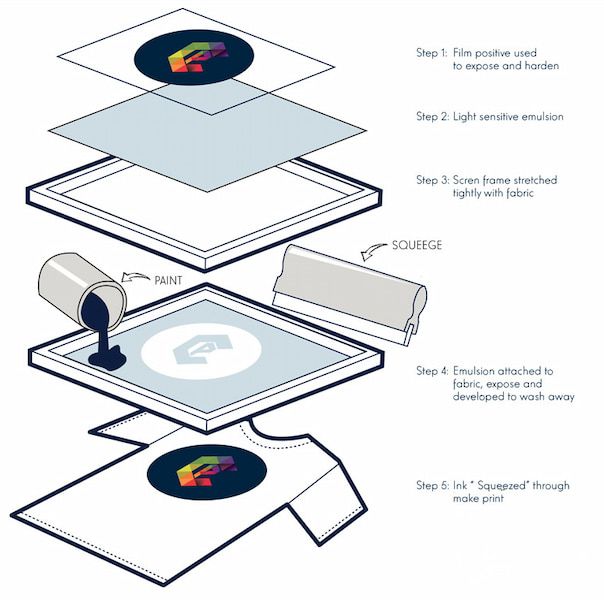
In the Screen Printing process, a rectangular frame has a mesh screen. On that screen, a custom stencil is placed up on the mesh screen. Place the frame on the surface that you want to print on. Then the paint is poured over the stencil and the paint is pushed onto the surface in an up-down motion with the help of a squeegee.
What Is The Flexographic Printing Process?
Flexographic printing is based on the principle of impressions and ink transfer. The reason why it is called Flexography is because the press plate that has an impression on itself is flexible.
A flexible press plate was a new thing compared to its competitive counterparts which use a metal plate in Lithography printing or have a non-flexible mesh like in screen printing.
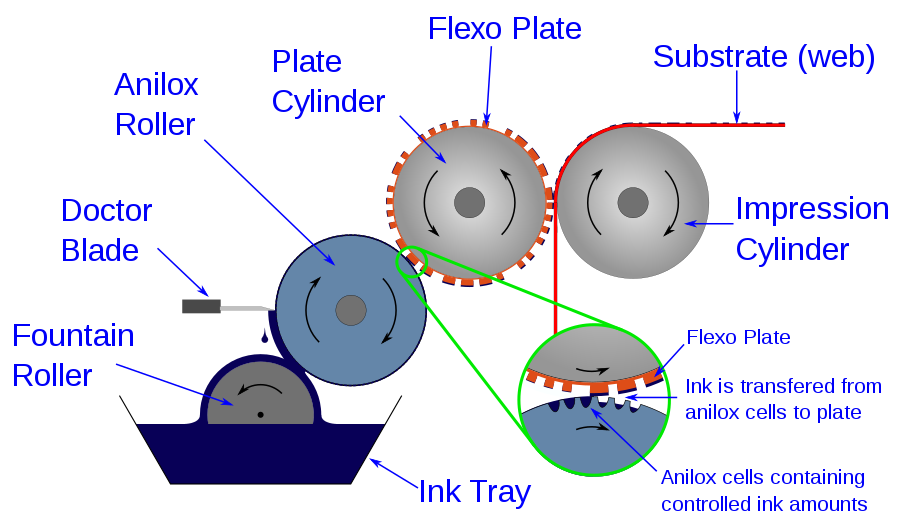
The process of flexographic Printing is written down below:
- The process starts with making a flexible press plate which is made from Photopolymer but in the early days, it was made from rubber.
- 3 main cylinders play an important role in flexographic printing. Their names are Anilox Roller, Plate Cylinder and Impression Cylinder.
- In the first step, we made a flexible press plate, now Before running the press we had to install the flexo plate on the Plate cylinder.
- After installation the press starts and ink is poured into the ink tray which has a fountain roller.
- This fountain roller is in contact with an anilox cylinder. So that the anilox cylinder gets ink on its surface.
- To make sure that the correct amount of paint is being transferred onto the anilox roller. A scraper-type tool called Doctor Blade scrapes off excess paint from the anilox roller.
- Now that the Anilox roller has just the right amount of ink on it. Another cylinder named plate cylinder that has a Flexo plate installed over its surface comes in contact with it. And the ink is distributed on the impressions.
- Then the flexo plate comes in contact with the surface which requires printing. This surface is called a substrate.
- Now the substrate is on the belt of the impression cylinder which puts enough pressure to get the impression.
- And the printing gets done on the media.
- Then it is dried and ready to use.
What Are The Advantages Of Flexographic Printing?
In the previous section, we discussed the whole process of flexographic printing process. In this section, we will talk about the advantages of flexographic Printing.
Wide variety of Colours
In flexographic printing, we can use a wide variety of colour ink. Not just we can experiment with the colour. But also with the quality of the ink.
Flexo printing is the first choice for the labels on any product, especially food and hygiene. People who prioritise safety as well as creativity prefer Flexography Printing.
Versatile printing on the surface
When we want to do something creative with packaging. Many times people experiment with different textures and finishes if they want something that will help with making impressive printing then you should opt for Flexographic printing.
Best for flexible packaging
Flexible packaging is the top choice for companies who are looking for lightweight, trendy and durable packaging. Flexographic packaging works efficiently when printing labels and other forms of printing.
You can read more about flexible packaging here.
Different types of inks can be used
When we talk about pollution caused by packaging we will come across the stats that more than 94% of the world’s total waste management.
Not just the plastic, but the inks used to print on them pose a threat to the environment as it creates pollution on a microscopic level that pollutes the groundwater and microplastic is polluting ground at a staggering rate.
To sort out this problem printing and packaging industry has come up with the environment-friendly ink that will pollute our environment.
However, the problem with eco-friendly ink is that you cannot use them on any printing press. This is where you can use flexographic printing as it can print with a variety of inks without any problem.
High quality
The consistency is real when we are talking about flexographic printing. This printing method is great if you want to get polished looking packaging, especially the labels and the outer packaging of products.
Economical
Something that makes Flexography perfect for commercial printing is its cost-effectiveness. The higher the volume of print media, the lower the cost for each print. Hence, it is a great option for commercial printing.
What Are The Advantages Of Screen Printing?
In the previous section, we went through the advantages of flexographic printing. In this part, we will talk about the advantages of screen printing in the following list:
Highly customisable
In screen printing, you can get customised products in premium quality as the technique used in screen printing allows a lot of room and chances for customization.
As well as you can go for bright, versatile and colourful inks which is great if you want to have a witty and catchy design.
Durable and long-lasting
The ink is spread in thick layers and the quality of the prints gets better. Along with that, it contributes to the printing being long-lasting and durable.
Printable on various surfaces
Just like flexography, you can print on a variety of surfaces with the help of screen printing as the frame can be used to print on hard to reach and print surfaces.
What is the best type of printing for packaging?
So which one would be the best pick for you? Well, if you want to get consistent prints and have high volume printing needs then you should go for flexographic printing.
But if you are more focused on quality rather than quantity. If you have more needs to get custom material then you should opt for screen printing.
You can take help from the benefits's list to see which one is better for you.
That’s all we have to say regarding these printing techniques.
Thank you for reading til the end.

Suman Mandal has been in the packaging industry for a long time. She is passionate about the innovative ways this industry comes up with. Currently, she is writing for To The Packaging about various packaging solutions.